工場訪問:ミツトヨ 志和工場(広島県東広島市)
原点回帰 国産の力で挑む
マイクロメータ生産で圧倒的世界トップ
生産効率追って、現場力重視のスマートファクトリーへ
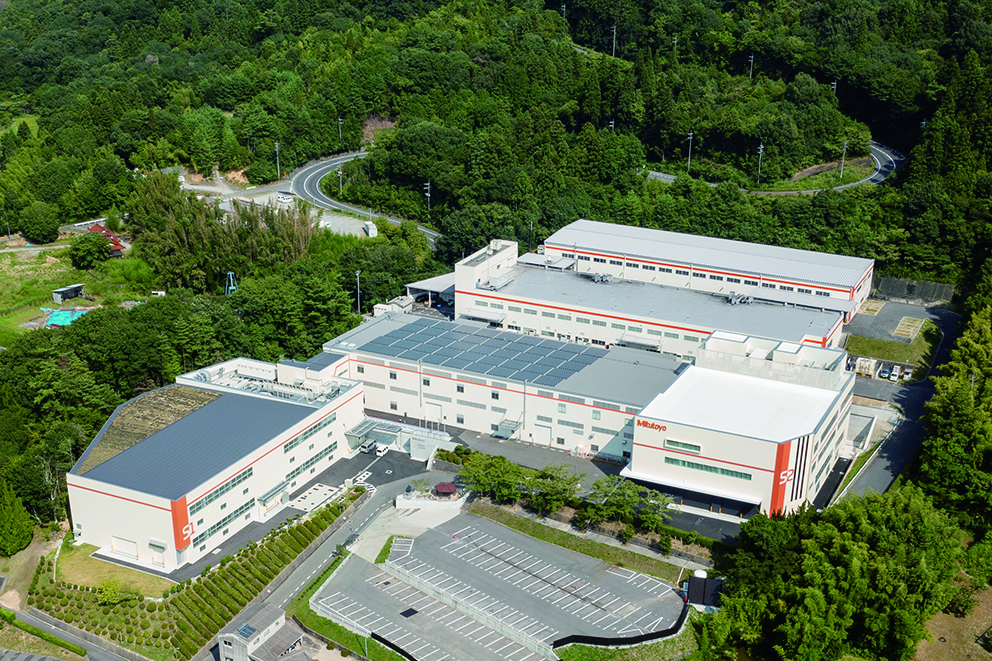
「マイクロメータの国産化を目指す」――。そう強い意志と明確な目的をもってミツトヨの創業者・沼田恵範氏が事業の第一歩を踏み出したのは1934年(昭和9年)のこと。そこから、同社は世界最大級の測定機器メーカーへ駆け上がっていった。紛れもなく「マイクロメータ国産化の夢」が原点だった。
ミツトヨが初めて国産化に成功したマイクロメータ(1936年)
その創業時から90年近くを経ていま、不思議な巡りあわせだが、同社のマイクロメータは、創業者の生家である浄蓮寺(東広島市)に隣接する志和工場が全数を生産する。生産量は業界トップ、いや世界断トツである。
ミツトヨは近年になって海外生産から順次撤退し、現在はごく一部の輸入部材を除き測定機器生産のすべてを国内10工場で担う形に変えている。
「国産で勝負する」という社の方針に沿ったものだが、そのなかで志和工場もまた、国産工場としての戦力強化に精力を傾注してきた。結果、創業の志が息づくスマートファクリーへ変貌しつつある。
現状の床面積で挑む 「生産キャパ倍増計画」
マイクロメータは、ねじの回転を利用して精密な長さを測定するツールだ。手軽に1000分の1㍉の精度で測れるため製造現場で欠かせない。ミツトヨではもっと高精度な、0.1マイクロメートルの精度測定を可能にした商品も揃える。同社がこの分野で圧倒したシェアを持つことは業界で知られる。
国内マイクロメータ市場は、推定シェア10%ほどの安価輸入品を除き、同社がほぼ独占。ミツトヨ製の生産は志和工場が一手に引き受けているのだから、志和工場が国内シェア9割を持つと言い換えていい。取材時、では世界市場での志和工場のシェアは? と聞くと「おそらく4割前後でしょう」と返ってきた。
それでも近年、実は志和工場で生産能力強化が大きな宿題になっていた。
「生産のキャパが足りない!」―。そう志和工場で悲鳴が上がったのは2018年、測定機器マーケットが過去最大で需要を伸ばした時だった。
この年から志和工場の指揮を取る藤川勇二志和工場長は「工場長になって当初の仕事は何より生産力を上げることでした。伸びる需要に全然追いついていなかった」と述懐する。
生産力強化に向け、敷地内にある計4つの工場のなかの、第1工場と第2工場(南棟)で増設を計画し昨年6月完成させた。全体のリニューアルも行った。
その後、後述するライン改革などを通じ生産キャパの拡大を進めている。
生産能力は今年中に18年のピーク比120%を目指す。さらにステップ2として25年には同160%、最終目標年度の29年には同185%にトライする計画だ。藤川工場長は「(29年には)出荷金額ベースでピークの2倍にしたい」と言葉を足した。
驚くことに同社は、この大幅な能力増強計画において、工場床面積は現状から拡大しないことを前提にしている。つまり、現有スペースのまま効率を上げ、ピーク比ほぼ倍にまで生産量を上げるということだ。
「まず今年の目標ですが、達成まで今はもう少しです。29年の最終目標まで必ずやり遂げて見せますよ」。藤川工場長から強気の笑顔が出た。
同期化・整流化を軸にした工場改革
「生産能力拡大がミッションでしたが、単に生産力を高めるのではなく、智恵を入れて新しいものづくりにチャレンジしようと取り組んできました」(藤川工場長)。
マイクロメータと協働ロボットでマイクロメータの部品を測定するユニークな自働装置はアイデアから生まれた
生産の「量」を追うとともにモノづくり改革に向けた策を連続的に打ち出した。「随分思い切ったこともやって、会社にも無理を言いました。今振り返って、よく会社が認めてくれたものだと思いますよ(笑)」。
数多いチャレンジのなかでも、各加工ラインのレイアウトを、最終の組立工程へ最短距離でつながるよう大幅に変えたことが特筆される。「すべての工場の部品、製造物が直線的に組立工程へ流れるようにした」(同)のだ。これにより、仕掛品などの無駄な滞留は従業員の目に明らかになり、余分な生産を減らし、余計な動作を抑え込めた。ライン改革について志和工場では「組立との同期化・整流化を徹底して進めたわけです」などと説明する。
ここで歴史をさかのぼり、志和工場が当初から「同期化・整流化」で優位性を持っていたことに少し触れたい。
志和工場がマイクロメータ専門工場として操業したのは1987年。小高い丘の斜面をだんだんと登るような形に建てられた。その概観をざっくり示したのが下の図だ。もうお気づきの方もいらっしゃるだろう。「隣り合う工場の2階と1階を意図して同じ高さにした」のが志和工場の最大特徴になる。これが当初からメリットを生んだ。
「1階で部品を加工し、隣接する工場の2階フロアに最短の直線移動で供給できる」がひとつ。「2階で組み立てた製品を、2階からトラック出荷できる」ことも効率を生む。付け加えれば、半地下の1階は室内の温度変化が少なく、精密機器の生産に持ってこいだ。
さてここで、近年実施してきた「組立との同期化・整流化を目指すライン改革」が求めたものと、志和工場の当初からの特徴が似ていることに気づかされる。
近年の取り組みは、元来優れた「動線」を持つ志和工場の強みを、さらに伸展させたものとも言えそうだ。
現場力とアイデアがスマファを支える
各工程では自動化やデジタル化を積極的に進めている。最終工程においては自動組立ラインを設計導入。また上流の機械加工では、量産加工で徹底したロボット化・自動化を進めた一方、多品種少量部品加工では、工作機械のそばに3次元測定機を設置し、加工と測定の両工程をつなぐ形で効率よく全数検査を行なうスタイルなどが見られた。
またMES(製造実行システム)を導入してのデジタル管理では、膨大な情報をLANでつなぎ、工程を超えた全体最適を生み出している。例えば加工工程にある工作機械の動きの変動を、次工程の測定データから読み取って補正するといった方向など。このようにスマートファクトリーとしての武装も着々だ。
それと人のアイデア、現場力の貢献度が見逃せない。効率や安全性向上を目指した社員の取り組みでは、各工程を担当するチームが改善テーマを決めて実行し、継続的に社内発表を行なっている。不断の改善が効率性や安全性を高める。
ロボットによる量産加工の完全自動化や、少量部品加工におけるラインサイトでの全数測定検査など、工場内は改革が進む
工場を案内してくれた藤川工場長が立ち止まり「これクレイジーでしょう」と指を差して笑った。見ると、マイクロメータの円筒状の部品(小さなスピンドルなど)の外径を、既に完成したマイクロメータが自動測定していた。協働ロボット&マイクロメータによる自動計測装置だ。藤川工場長が言う「クレイジー」とは、斬新すぎるという意味だろう。若手技術者のアイデアから生まれたこの自動計測装置は、目下3号機まで進化し生産の場を支えているという。
「みんなが改革に熱心で、熱意があるから成果と同時に感動も出てくる」と藤川工場長。最後、チャレンジャーの目で次のように加えた。
「工場稼働日はおよそ1カ月に20日。これまでマイクロメータのリードタイムは40日、つまり2カ月掛かっていましたが、10日に縮減してみせます。それと最も大事なことですが、当社の強さは比較精度でなく絶対精度であること。国家基準とのトレーサビリティを維持した中で測定機器を市場へ提供しているため信頼性で勝ります。つまり生産効率を上げる私たちの取組みによって、世界断トツの今の位置をさらに上へ伸ばせると思います」。
(2022年9月25日号掲載)